Kent, Ohio. Since 2014, the Theodore Roosevelt High School Manufacturing Technology Program in Kent, Ohio has trained hundreds of aspiring CNC programmers, machinists and engineers for successful careers in the manufacturing industry. Troy Speer, a specialist in computer-aided design and engineering, advanced carpentry, and basic wood and metalworking at Theodore Roosevelt High School, also known as Kent Roosevelt High School, has been in the career program for the past 13 of his 24 years of study. . As technology and industry have changed over the decades, Speer's teaching responsibilities have also changed.
"I grew up in this position," he said. "I started giving basic carpentry lessons and then took them into the 21st century."
In 2009, with the support of the then superintendent and his former teacher, Speer asked the district to invest in a CNC milling machine. The lawsuit was successful and the investment continues to pay off. In subsequent years, under the guidance of teachers, students built everything from fully equipped kitchens for community members to computer cabinets for the district, chairs for children and furniture for the district nursery schools.
Kent Roosevelt's woodworking, carving, and joinery program was the only one of its kind in Ohio. Unfortunately, due to budget constraints, the Ohio Department of Education has canceled this program. Although the industry-backed CTE woodworking program ended in 2013, Spear soon found a silver lining.
"Completing the woodworking program helped me transition into an apprenticeship," he said. “What I am doing now is the result of this woodworking industry. Now everything is in production, much more than before ”.
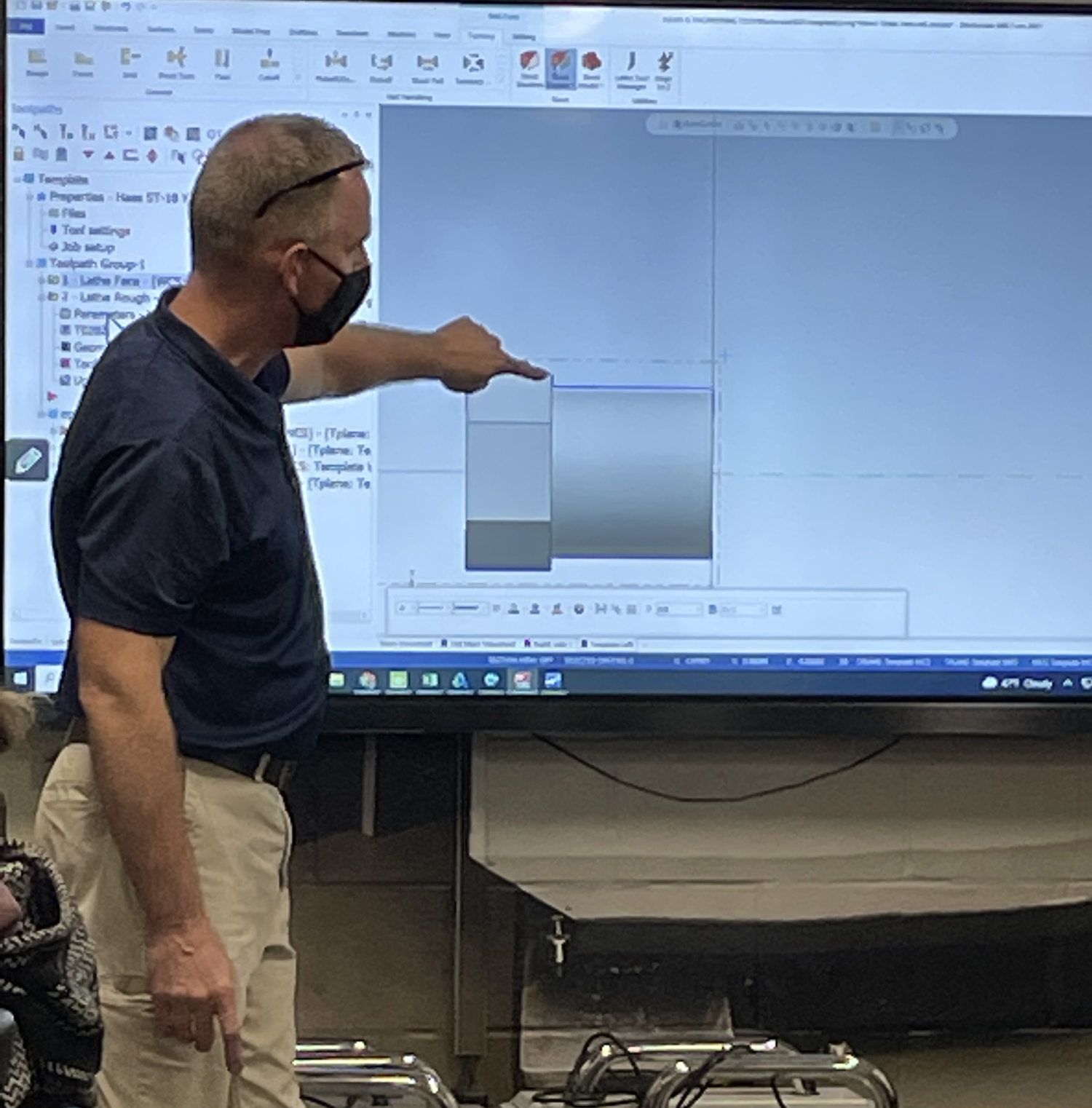
The Kent Roosevelt High Manufacturing Technology program, launched in 2014, enrolls elementary and middle school students from five other local and Kent school districts. In the Computer Science and Design program, students use software and hardware to create shop drawings, 3D solid models, parts, and assemblies. Laser engravers, 3D printers, mechanical and CNC machines allow you to make parts in metal, wood and plastic.
Young people are first introduced to manufacturing by studying metrology and metrology. Armed with steel micrometers and rulers, they learn measurement systems and decimal equivalents that line up with detailed drawing lessons. Based on these core skills, students with versatile skills excel in a hands-on curriculum.
"A graduate student can enter any Ohio public institution for undergraduate or post-secondary education and bring a three-credit course in line with a CAD-related course," Speer said. "There is a second course that covers manufacturing operations."
From the fundamentals of machine tools to CAD / CAM
At the beginning of the program, Speer focuses on measurement and drawing, bringing these topics together to help teens understand how to calculate decimal equivalents and transfer that knowledge to a CNC or machine tool. Although CNC technology is a major focus of Kent Roosevelt's manufacturing program, students should be familiar with the basics of machine tools.
"Many local employers claim they have hired adults directly from CNC schools who don't understand decimals or moving factors," Speer said. “All our industrial partners ask us to teach manual machining, even if they use CNC more than anything else. They all still have the manual handling of fonts for the different components. "
After learning the basics of manual machining, Speer introduces the CNC, shows the controls, and helps students familiarize them. They learn how to set up a machine, load parts, create cross references and run machining programs. This is where Mastercam CAD / CAM software (CNC Software, LLC) comes to the rescue.
In a series of lessons, students work on drawings, starting with 2D drawings created with CAD software. They switch to 3D drawing and begin to develop their visualization skills. Then they learn 3D solid modeling and Solidworks.
"At this stage, students can appreciate the power of Mastercam and all of its features," said Speer. “They can take this 3D solid model, superimpose the toolpath on it, generate a G-code, bring it to our lab, load it with material and touch the tools. They load a G code created in CAD / CAM. Through this process, they know, understand and are able to translate the code as it runs on the machine, creating the details. "
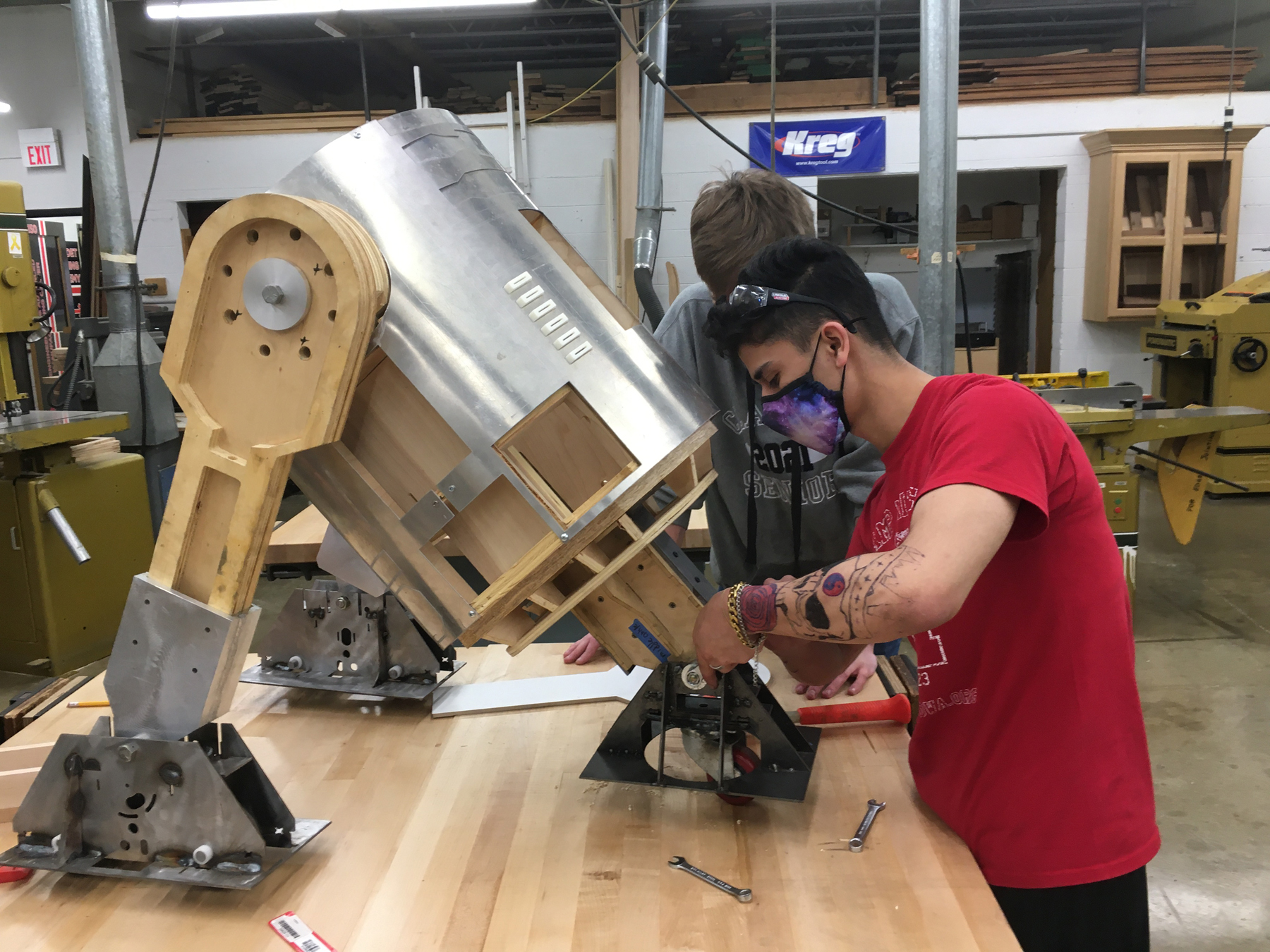
Kent Roosevelt's mechanics include a Clausing lathe with a 13-inch motor and a Bridgeport machine. There are also band saws in the production center. Haas TM1 CNC router; Haas TL1 lathe; Haas ST10 turning center; Wardjet water cannon; Lincoln Electric RealWeld Coach; and Omnitech Selexx Pal CNC milling machine.
"We made a commitment upfront to always use industry tools, not educational opportunities," said Speer. "It's not like there's anything wrong with these types of machines, but our goal is to introduce students to industrial machines and make them easy to use."
The computer lab, located next to the machine building and woodworking workshop, includes 18 computers and instructor seats, all equipped with Mastercam software. Here students learn about the powerful and exciting relationship between software, design, programming, and processing. Students have access to 10 different brands of 3D printers to prototype their designs.
"The first step is to try to connect them and show them that the software is going to be very straightforward and methodical," said Speer. “Then we go step by step to the arrow. we have something. Then we go back and work on Mastercam ".
dynamic motion technology
Lance teaches wireframe, drawing and geometry creation. Last year the class worked on a pole made from a 2 "x 3" block of aluminum. The piece included a round hexagon with holes drilled in each of the hexagonal corners, as well as two triangular pockets. Each of the drilled holes was tapped with a 1/4 inch - 20 tap. The students used different tools to create the widget. They drew the part in both wireframe and Solidworks, then imported it into Mastercam and created toolpaths. Solidworks student drawings were used to 3D print the parts.
"The class was introduced to dynamic motion technology, especially dynamic milling, with this small hexagonal part," said Speer. “I would like to thank the distributor Mastercam FASTech Inc. I cannot thank you enough for the help we have received. Kevin Richardson, Scott Hardy, Josh Chopp and the rest of the team are doing a phenomenal job.
“Introducing students to Dynamic Motion was a lot of fun because we didn't cut out too much material. What we did was clipped, removed quickly and easily. "
After completing the widget design, each student had an aluminum version of the printed part, a wired version drawn and programmed, and a rigid 3D model. Different models of the same product showed the diversity and creativity of the production.
Once students understand the basics of design, programming and machining, Spear will be sure to emphasize the importance of machine simulation, which demonstrates the cutting process on a virtual copy of the machine. This ensures safe and accurate creation of toolpaths and avoids machine collision before parts are machined.
"I really enjoy teaching students how to use Backplot and Verification so they can simulate or see how the machine will cut," he said. “Thanks to FASTech, we have a machine environment where we can see the virtual ST10 in action. We can open and close doors and watch the crack turn. The tower turns. You can see if an accident is happening or if a reduction is possible. "
droid project
In addition to building small parts, like the widget above, the various classes in the building program work together to design and develop large-scale projects, including a full-size remote-controlled robot. Called Project Droid, this multi-class project was inspired by a popular science fiction character and continues to be a hit with students.
Before the idea of creating a droid, students made lightsabers. The torch handles have been specially designed; The handles covered the 3D printed wings. The project turned out to be so exciting and successful that the students decided to create their own version of the famous movie droid. The toy droid, powered by an electric car engine, was the brainchild of four different classes that ran for four years. The last class to work on the robot called it R5-V7.
First grader Speer drew and designed plywood parts in Solidworks, learning how to assemble, design and cut them on a CNC router. By the end of the year, they had assembled a droid.
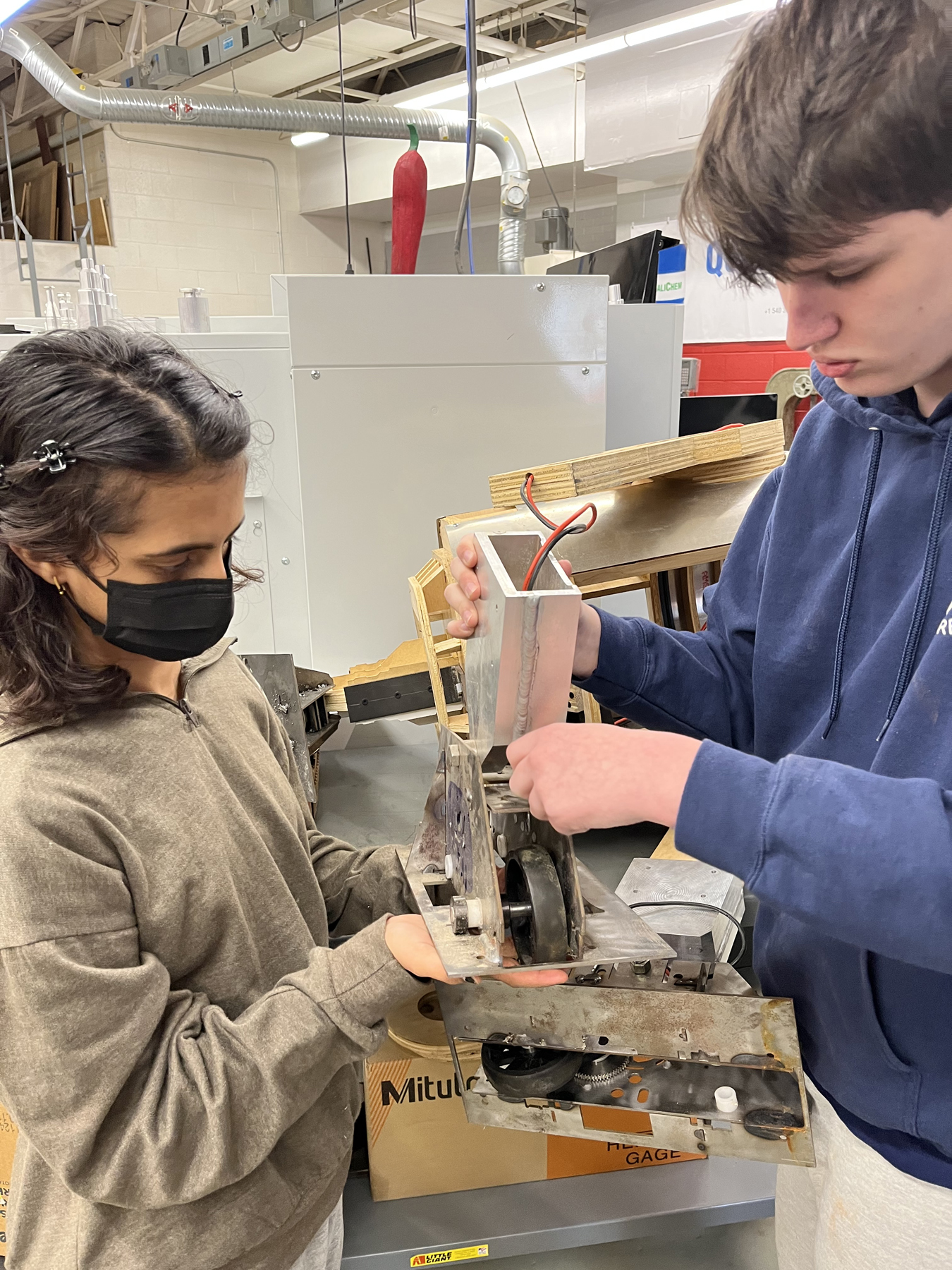
The following year, the students saw Project Droid in the recruiting process and were ready to participate. They designed and fabricated the leather using Wardjet waterjet cutting and aluminum foil, as well as 3D printed accessories. The students cut and welded the legs that held the wheels and motors.
Jeff B., Speer's co-teacher, asked his superiors to work on the ankles that connect the legs to the wooden legs. Bee was able to incorporate dynamic milling into this class as they opted for a thick aluminum outer pocket to round off the lower leg of the droid.
Work skills
While Kent Roosevelt High School faculty focus on classroom projects and teach software, computers and development skills, another group of individuals play a key role in preparing students for employment opportunities. The Local Producers Advisory Board provides information on which skills are important to the entry-level workforce. In addition to sharing industry knowledge, the partners take Spears and her students on a tour of their manufacturing facilities and present them with future career opportunities. In the spring, company representatives are invited to Kent Roosevelt High School to participate in mock interviews with younger students.
"I tell my students that there is potential work behind every fake interview," Speer said. “Last spring we had an explosion of requests from people we had never heard of in the industry before. They said, "We heard you have a plan. We need workers. Who do you have? We want you today."
During the interview, students can let the industry partner know that they may be interested in a future job and ask the interviewer to keep their resume. This experience offers networking opportunities and the opportunity to work during the summers and do a high school internship. Paid internships are combined with credits for the Manufacturing and Technology course.
Theodore Roosevelt High School's computer engineering and design students have been successful since graduation. Thanks to the school's comprehensive curriculum, they are well prepared for a career in manufacturing. One area both Speer and Bee hope to add to the curriculum is model building. The school already has a plastic injection molding machine, so the next logical step is to teach students how to use it. Given the high school location, preparing future programmers and machinists for a career in the plastics industry is a thoughtful and forward-thinking program.
"Our state corridor is a huge corridor of mold," Speer said outside his school in Akron. “With our injection molding machine, we hope to introduce students to mold making and design. This really goes for the Dynamic Motion technology that Mastercam is famous for. This is an industry that we look forward to. "
Source: Masterkam. Visit mastercam.com for information.